Introduction:
Exoskeleton technology has emerged as a revolutionary solution in the construction industry, offering enhanced safety and improved worker performance. These wearable robotic devices provide support, stability, and strength, reducing the physical strain of manual labor tasks. From reducing the risk of musculoskeletal injuries to enhancing productivity, exoskeletons transform how construction professionals work on job sites.
Manufacturing Process: Bringing Exoskeletons to Life
The manufacturing process of exoskeletons involves several key steps, including design, fabrication, assembly, and testing. Each step is crucial in creating functional and ergonomic exoskeletons that meet the needs of construction professionals.
Let’s delve into the process:
- Design and Engineering: The journey begins with the design and engineering phase, where the exoskeleton’s form and functionality are meticulously planned. Designers use specialized software to create detailed 3D models, considering factors such as the tasks the exoskeleton will assist with, range of motion, and user comfort. Iterative design improvements may occur based on feedback from users and ongoing research.
- Material Selection: Suitable materials are selected for each exoskeleton component once the design is finalized. These materials must balance strength, durability, and lightweight properties. Common choices include light alloys, carbon fiber composites, and high-strength plastics. The selection ensures that the exoskeleton is robust enough to withstand the forces encountered during construction tasks while remaining comfortable for extended wear.
- Fabrication of Components: The fabrication stage brings the design to life. Depending on the chosen manufacturing techniques, components may be produced through CNC machining, 3D printing, or injection molding processes. CNC machining is often utilized for metal parts, ensuring precision and strength, while 3D printing or injection molding can create complex geometries for plastic or composite components.
- Assembly: Once the individual components are fabricated, they are carefully assembled to form the complete exoskeleton. Joints, hinges, straps, and other hardware are securely attached, considering factors such as adjustability and user ergonomics. This stage also involves integrating sensors, actuators, and control systems that enable the exoskeleton to respond effectively to the user’s movements.
- Integration of Power and Control Systems: Exoskeletons may require power sources and control systems depending on the specific design. Batteries or power packs, electric motors or actuators, and a network of sensors are integrated seamlessly into the exoskeleton. These components work harmoniously to provide user support, strength, and real-time feedback.
- Ergonomic Adjustments: Exoskeletons are designed with user comfort in mind. Adjustable elements such as straps, buckles, and fasteners allow users to customize the fit and optimize the exoskeleton to their unique body proportions. These adjustments ensure a snug and secure fit, enabling the exoskeleton to distribute forces and effectively support the user’s movements.
- Testing and Quality Assurance: Rigorous testing and quality assurance procedures are conducted before exoskeletons are ready. Load, stress, endurance, and usability testing are performed to ensure the exoskeletons meet safety standards and performance requirements. User feedback and field testing may lead to iterative design improvements, refining the exoskeleton’s functionality and addressing any identified issues.
By following this meticulous manufacturing process, exoskeleton manufacturers can produce high-quality, ergonomic, and practical solutions for construction professionals. Carefully integrating design, materials, and advanced technologies ensures that exoskeletons can enhance worker safety and performance in demanding construction environments.
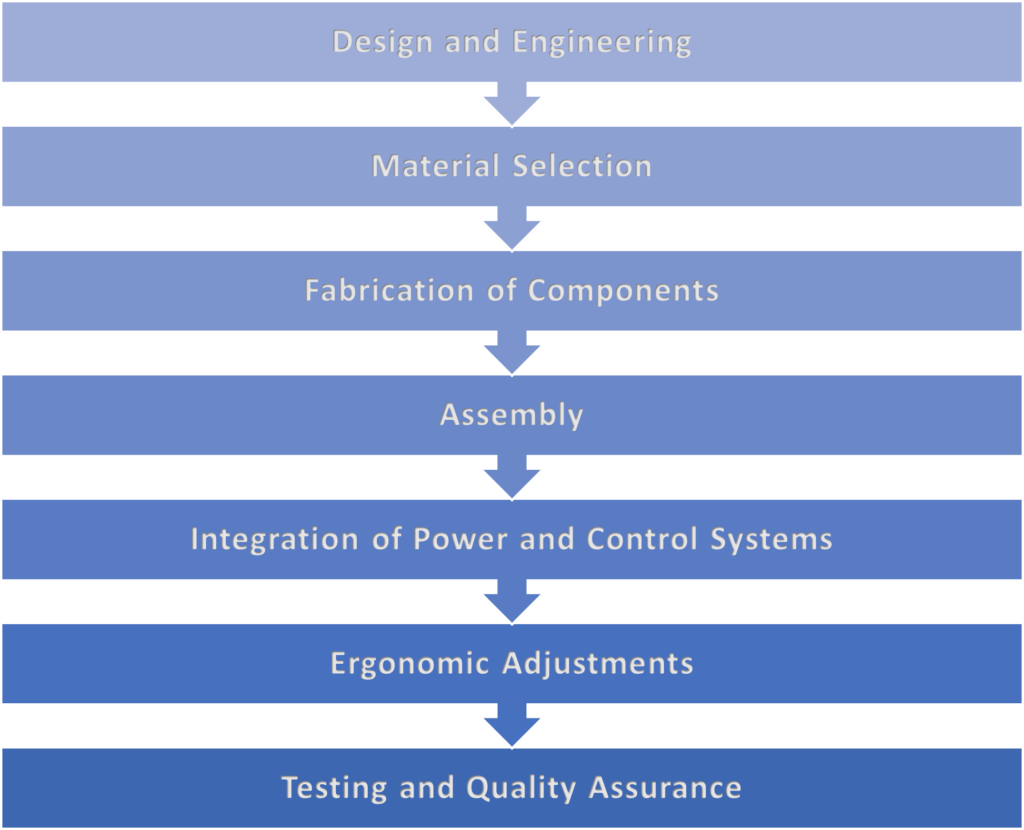
Enhanced Worker Safety and Injury Prevention:
Exoskeletons are designed to provide physical support to workers, particularly during tasks that involve heavy lifting, repetitive motions, or prolonged periods of exertion. They promote proper posture and biomechanics, ensuring workers maintain optimal alignment and reducing the risk of overexertion. By reducing the strain on the musculoskeletal system, exoskeletons can help prevent injuries such as strains, sprains, and fatigue-related incidents.
Increased Worker Efficiency and Productivity:
Exoskeletons are particularly beneficial for tasks involving repetitive motions or heavy lifting, allowing workers to maintain energy levels and work consistently throughout the day. Exoskeletons enable workers to perform tasks with less effort and fatigue by augmenting human strength and endurance. This increased efficiency improves productivity, as workers can accomplish more in less time.
Versatility and Adaptability:
Exoskeletons come in various forms, ranging from full-body exoskeletons to devices that focus on specific body parts, such as the back or arms. They can be customized to fit individual workers and accommodate job requirements. This versatility allows construction professionals to choose the appropriate exoskeleton, ensuring optimal comfort, mobility, and functionality.
Integration with Existing Workflows:
Exoskeletons are designed to integrate into existing work processes seamlessly. They are lightweight, ergonomic, and easy to wear, allowing workers to move freely and perform tasks without hindrance. Exoskeletons can be quickly donned and doffed, minimizing disruption to workflow and enabling efficient transitions between functions.
Real-world Applications of Exoskeletons: Case Studies Demonstrating Benefits in Different Industries
Exoskeleton technology is finding real-world applications across various industries, revolutionizing work environments and enhancing worker well-being. Through case studies conducted in different locations, the benefits of exoskeletons have been demonstrated in improving productivity, reducing fatigue, and enhancing safety.
In a large-scale construction project, exoskeleton technology was implemented to address worker fatigue and improve safety. The exoskeletons were designed to support workers during heavy lifting and repetitive tasks, reducing the risk of musculoskeletal injuries. Workers involved in material handling and overhead work wore the exoskeletons throughout their shifts. The lightweight design and adjustable features allow for a comfortable fit and freedom of movement. The exoskeletons significantly reduced muscle fatigue and strain by redistributing the load and assisting the workers’ upper body. The implementation of exoskeletons resulted in notable improvements in worker productivity and safety. Workers reported reduced discomfort and fatigue, enabling them to work longer without compromising their well-being. The incidence of work-related injuries related to lifting and repetitive tasks decreased, positively impacting the overall safety record of the project.
Meanwhile, exoskeletons were introduced to improve worker efficiency and ergonomics during assembly line operations. The facility experienced challenges with workers experiencing muscle fatigue and discomfort due to repetitive motions and awkward postures. The exoskeletons implemented in this case were specifically designed to support the workers’ upper body and arms. By reducing the strain on the muscles and joints involved in repetitive tasks, the exoskeletons enhanced worker endurance and reduced the risk of repetitive strain injuries. Workers reported increased productivity as they could perform tasks more efficiently and with reduced effort. The exoskeletons provided a supportive framework, allowing workers to maintain proper alignment and reducing the risk of fatigue-related errors. The improved ergonomics and reduced physical strain contributed to a more comfortable work environment and overall worker satisfaction.
These case studies exemplify the tangible advantages of exoskeleton technology, showcasing its potential to transform work practices and create a more sustainable and safe work environment.
Comparing Exoskeletons to Traditional Methods: Data on Efficiency, Safety, Cost, and Productivity
Exoskeletons offer a promising alternative to traditional methods in various industries. By analyzing data on efficiency, safety, cost, and productivity, we can gain insights into the advantages of exoskeleton technology. The data highlights the transformative impact of exoskeletons, making them a viable solution for enhancing work processes and worker well-being. Exoskeletons have shown the potential to improve work efficiency by reducing physical strain and fatigue. They also contribute to enhanced safety by minimizing the risk of musculoskeletal injuries and fatigue-related incidents. While initial investment costs may increase, exoskeletons lead to long-term savings through reduced workers’ compensation expenses and increased productivity. By providing support, exoskeletons enable workers to perform tasks more consistently and accurately, improving overall work quality.
Future Advancements and Potential:
As exoskeleton technology advances, we expect different design, comfort, and functionality improvements. Advanced sensors and actuators may enable exoskeletons to adapt to the wearer’s movements more intuitively, providing outstanding support and enhancing the natural range of motion. Integrating intelligent technologies like data analytics and artificial intelligence could improve safety features, monitor worker fatigue levels, and provide valuable insights for optimizing work processes.
Conclusion:
Exoskeletons are revolutionizing the construction industry by enhancing worker safety, improving performance, and increasing productivity. With their ability to reduce the risk of injuries, minimize physical strain, and support workers during physically demanding tasks, exoskeletons have become valuable tools for construction professionals. As technology continues to evolve, exoskeletons hold the potential to become indispensable in construction, contributing to safer and more efficient work environments. By embracing this innovative technology, the construction industry can ensure the well-being of its workforce and lay the way for a more productive and sustainable future.